Commercial roofing for warehouses demands specialized solutions to address the unique challenges of large-scale industrial structures. These roofing systems must possess substantial load-bearing capacity, often supporting up to 150 pounds per square foot, while demonstrating exceptional weather resistance against harsh elements. Durability and longevity are paramount, with options like built-up roofing and metal roofs offering lifespans of 50 years or more. Energy efficiency improvements, such as reflective materials and proper insulation, can greatly reduce operational costs. Regular maintenance and tailored emergency response plans are vital for preserving roof integrity. The following sections explore the intricacies of warehouse roofing solutions in greater detail.
Roofing Highlights
- Warehouse roofs require high load-bearing capacity, with metal roofs supporting up to 150 pounds per square foot.
- Durability against harsh weather conditions is crucial, with options like modified bitumen and metal roofing offering excellent resistance.
- Longevity is paramount, with metal roofs lasting 20-50 years and built-up roofing systems potentially enduring for 50+ years.
- Energy-efficient roofing materials can decrease cooling costs by up to 50% and support sustainability goals.
- Regular maintenance and inspections are essential to preserve roof integrity and extend lifespan, with some systems needing checks only every 10-15 years.
Warehouse Roof Durability Requirements
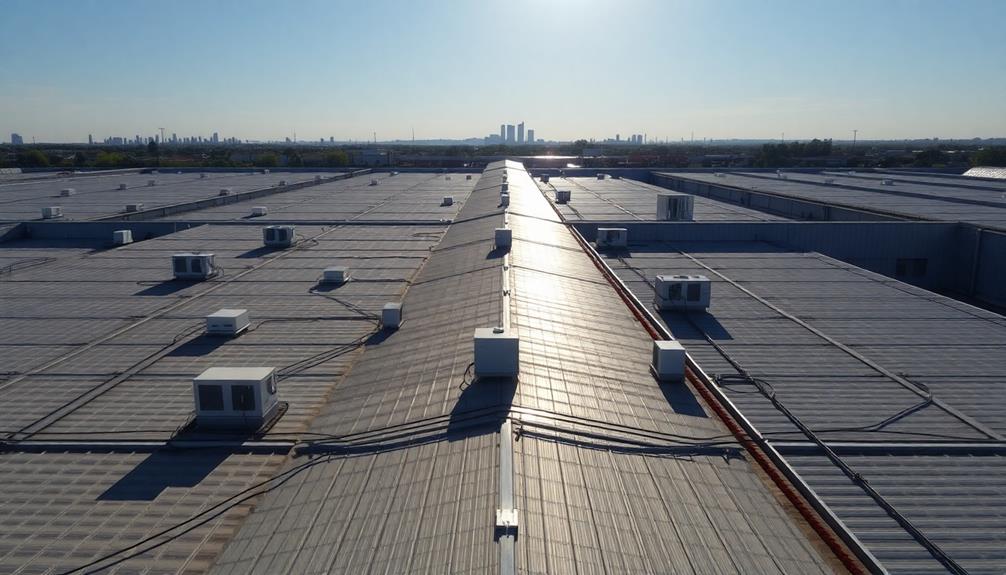
At Commercial Roofing Solutions, we ascertain the unique durability requirements for warehouse roofs. Our team of experienced professionals specializes in installing and maintaining robust roofing systems designed to withstand the challenges faced by warehouses, including heavy foot traffic, extreme weather conditions, and potential impacts.
We offer a range of options, including modified bitumen, built-up roofing (BUR), metal roofing, and single-ply systems like TPO and EPDM. Our highly-skilled team is dedicated to providing affordable rates and ultimate quality assurance for all commercial roofing needs.
We pride ourselves on being a local, family-owned business operating in Colorado, guaranteeing personalized service and attention to detail. Our experts will assess your specific warehouse needs, considering factors such as foot traffic levels, exposure to elements, and maintenance requirements, to recommend the most appropriate roofing solution.
With our all-encompassing services, we safeguard your warehouse roof provides long-lasting protection and performance, helping you secure your valuable inventory and operations for years to come.
Load-Bearing Capacity
Certainly, the load-bearing capacity of a warehouse roof is a vital factor in its design and construction. Commercial roofing systems for warehouses must be engineered to support substantial weights, including heavy equipment, stored goods, and potential snow loads. This guarantees the structural integrity of the building and the safety of its contents and occupants.
When selecting a roofing system for a warehouse, it’s necessary to consider materials that can withstand significant live loads. Modified bitumen and built-up roofing systems are popular choices, capable of bearing up to 100 pounds per square foot. For even greater load-bearing capacity, metal roofs, particularly standing seam metal roofs, can support loads up to 150 pounds per square foot, making them an excellent option for many warehouse applications.
To decide on the most appropriate roofing system for your specific warehouse needs, consulting a structural engineer is imperative. They can assess the unique requirements of your facility and recommend a roof type that meets or exceeds the necessary load-bearing capacity. Proper installation and regular maintenance of the chosen roofing system are equally important to ensure its long-term performance and structural integrity throughout the warehouse’s lifespan.
Weather Resistance
Storm clouds looming on the horizon serve as a stark reminder of the vital importance of weather resistance in warehouse roofing systems. Commercial Roofs must withstand the harshest elements, from heavy snowloads to strong winds and extreme temperature fluctuations.
To guarantee the best protection for warehouses and their contents, facility managers must carefully consider the types of warehouse roofing materials that can endure these challenges.
Among the most resilient options are Modified Bitumen Roofing and built-up roofing systems, which offer exceptional durability against weather-related damage. A metal roof is another excellent choice, particularly in areas prone to high winds.
For those seeking alternative solutions, single-ply membranes like TPO and EPDM can be effective when properly installed and maintained. However, it is imperative to select roofing materials that are rated for the specific climate conditions of the warehouse’s location. This decision should align with local building codes and take into account the unique weather patterns of the area.
Longevity and Maintenance
Longevity and durability are paramount concerns when selecting roofing systems for warehouses. These industrial buildings require robust roof systems that can withstand the test of time and minimize maintenance costs.
The best roofing materials for commercial buildings often incorporate multiple layers, providing enhanced protection against the elements and prolonging the lifespan of the structure.
Metal roofs have emerged as a top choice for warehouses due to their exceptional durability and resistance to various environmental factors. This type of roof can last 20-50 years with proper attention, making it an ideal option for industrial facilities. Regardless of the chosen materials, regular inspections and maintenance are essential for preserving the integrity of any commercial building’s roof system.
Seamless, single-ply options like TPO and PVC offer excellent waterproofing capabilities, reducing the likelihood of leaks and subsequent damage. These materials are particularly well-suited for warehouses that experience heavy foot traffic or require reinforced membranes to support equipment.
Benefits
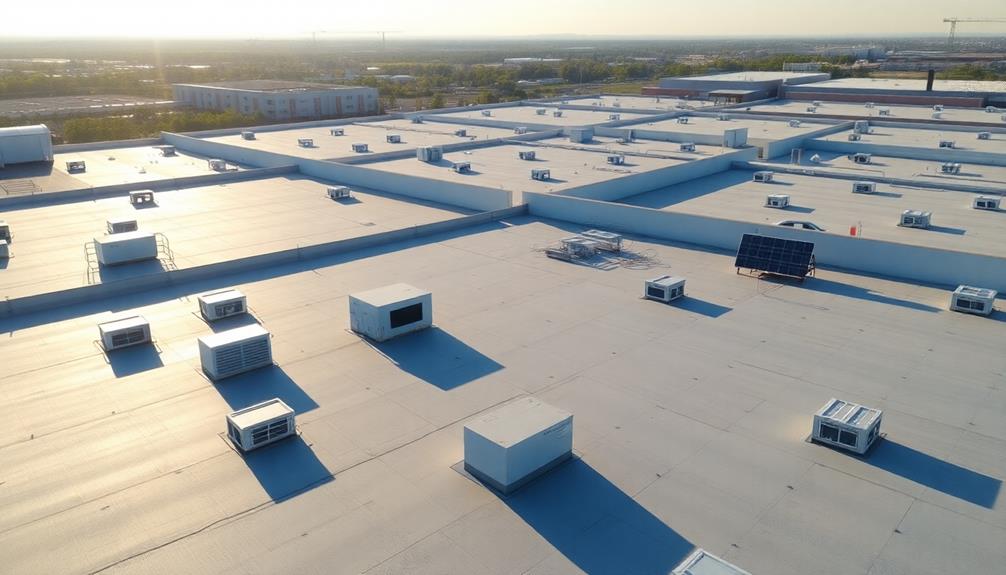
Commercial roofing systems for warehouses offer numerous advantages that contribute to the overall performance and cost-effectiveness of these facilities. The durability and longevity of modern roofing solutions guarantee long-term protection against harsh weather conditions and heavy foot traffic, minimizing the need for frequent replacements.
Commercial roofing experts can handle repairs and full replacements for any size job, ensuring exceptional quality and affordable pricing. Energy-efficient options can greatly reduce cooling costs, while low-maintenance requirements help decrease operational expenses over time, making these roofing systems a smart investment for warehouse owners and operators.
Durability and Longevity
When selecting a roofing system for warehouses, durability and longevity are paramount considerations. The type of roofing chosen can profoundly impact a facility’s long-term performance and cost-effectiveness. Various types of roofing systems offer different lifespans, with built-up roofing (BUR) and metal roofing standing out for their exceptional longevity. Properly installed BUR systems can endure for 50 years or more, providing robust waterproofing capabilities and adaptability to diverse climates. Metal roofing, when expertly installed and maintained, can last an impressive 50 to 100 years, making it an excellent investment for warehouse owners.
Other roofing options also offer considerable durability:
- Modified bitumen roofing: Up to 20+ years of service life
- Single-ply systems (TPO, PVC, EPDM): 10 to 40 years, with EPDM potentially reaching 40 years
- Liquid-applied coatings: 10 to 25 years, enhancing roof restoration efforts
The longevity of a warehouse roof depends on a variety of factors, including state and local building codes, environmental conditions, and maintenance practices. By selecting the appropriate roofing system and ensuring proper installation, warehouse owners can maximize their investment and protect their facilities for decades to come. Regular inspections and timely repairs are essential for maintaining the roof’s integrity and extending its lifespan.
Energy Efficiency Improvements
Focusing on energy efficiency improvements, warehouse owners can substantially reduce operational costs and environmental impact through strategic roofing choices. Implementing reflective roofing materials, such as white membranes or coatings, can drastically decrease solar heat gain and lower cooling costs by up to 50% in some cases. These materials enhance the roof’s reflectivity and corrosion resistance, contributing to improved thermal performance and longevity.
Cool roofs and vegetative roofs are particularly effective energy-efficient solutions that minimize a warehouse’s carbon footprint while supporting sustainability goals. These roofing systems, characterized by high solar reflectance and thermal emittance values, can help facilities meet LEED or other green building certification requirements.
Additionally, proper insulation beneath the roofing system further enhances the warehouse’s thermal performance, leading to substantial energy savings on both heating and cooling.
Incorporating daylighting features, such as strategically placed skylights, can reduce the need for artificial lighting, further improving the warehouse’s overall energy efficiency. By combining these various energy-efficient roofing strategies, warehouse owners can create a more sustainable and cost-effective facility that aligns with modern environmental standards and operational best practices.
Low Maintenance Requirements
Beyond energy efficiency considerations, warehouse owners should also prioritize roofing systems with low maintenance requirements. Commercial roofing solutions that reduce upkeep can significantly decrease long-term operational costs and extend the lifespan of the structure. When evaluating which roof is best for a warehouse, it’s crucial to consider options that require infrequent maintenance, particularly for low slope or flat roof designs.
Several roofing systems offer excellent low-maintenance benefits:
- Metal and modified bitumen roofs often need inspections only every 10-15 years
- TPO and PVC roofing membranes are self-cleaning, lessening maintenance needs
- Built-up roofing (BUR) systems can last 20-30 years with proper care
- Liquid-applied coatings can be reapplied as needed, prolonging roof longevity
Steel roofing and single-ply membranes like TPO and EPDM are particularly well-suited for warehouses, as they combine durability with minimal upkeep requirements. To guarantee peak performance, warehouse owners should schedule an inspection with experienced professionals every few years. This proactive approach helps identify potential issues before they escalate, maximizing the roofing investment. By selecting a new roof with low maintenance needs, warehouse operators can focus on their core business activities while enjoying peace of mind about their building’s protection.
Roof Maintenance Scheduling Options
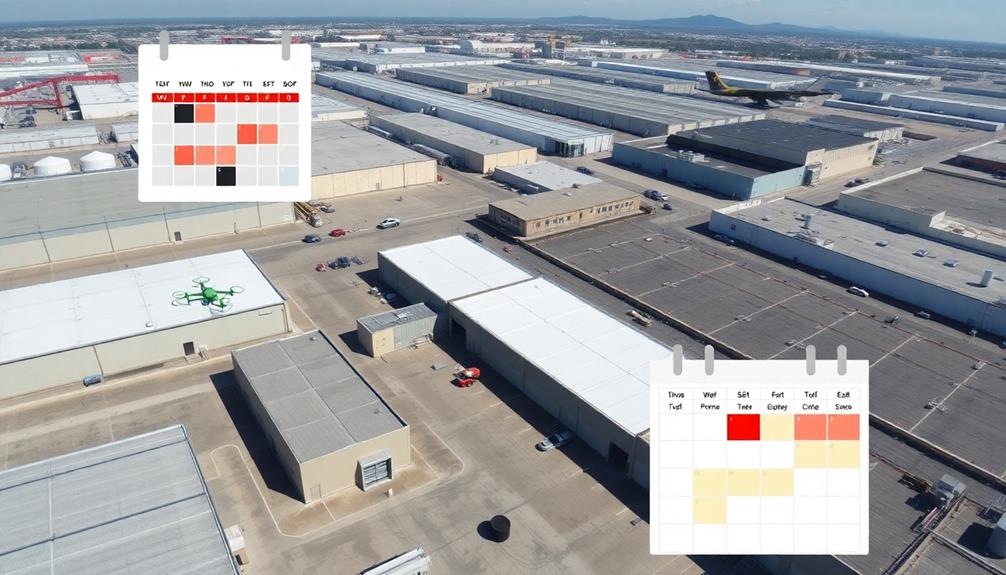
Effective roof maintenance scheduling for warehouses encompasses preventive maintenance plans, strategic seasonal inspections, and robust emergency response protocols. By implementing an extensive approach that addresses routine upkeep, climate-specific challenges, and unforeseen issues, warehouse operators can significantly extend the lifespan of their roofing systems. The following table outlines key components of a well-structured roof maintenance schedule, emphasizing the importance of proactive care and timely interventions:
Maintenance Type | Spring | Summer | Fall | Winter | As Needed |
---|---|---|---|---|---|
General Inspection | X | X | X | ||
Debris Removal | X | X | X | X | |
Drainage Check | X | X | X | X | |
Sealant Inspection | X | X | |||
Emergency Repairs | X |
Preventive Maintenance Schedules
A well-structured preventive maintenance schedule is essential for maximizing the lifespan and performance of commercial warehouse roofing systems. By implementing regular inspections and proactive measures, building owners can mitigate potential issues before they escalate into costly repairs. A thorough preventive maintenance plan typically includes:
- Bi-annual professional inspections of the roof deck and associated components
- Quarterly assessments of water drainage systems and debris removal
- Semi-annual application of protective coatings to enhance durability
- Ongoing documentation in a detailed maintenance log
These preventive maintenance schedules should be tailored to the specific roofing types and environmental conditions of each warehouse. Engaging a reputable roofing contractor to develop and execute this plan guarantees that all aspects of the roofing system are addressed systematically. Regular inspections allow for early detection of potential problems, such as punctures or leaks, which can be promptly repaired to maintain the roof’s integrity. By adhering to a consistent maintenance routine, building owners can extend the lifespan of their roofing systems, optimize performance, and potentially reduce long-term costs associated with major repairs or premature replacement. This proactive approach not only protects the physical structure but also safeguards the valuable inventory housed within the warehouse.
Seasonal Inspection Timing
To maximize the effectiveness of commercial warehouse roofing maintenance, seasonal inspection timing plays a pivotal role. For ideal roof performance, facility managers should conduct thorough inspections twice annually, ideally in spring and fall. These strategic timings allow for the assessment of existing roof conditions before the onset of extreme weather, enabling proactive measures to address potential issues.
The pros and cons of different inspection schedules must be carefully weighed, considering factors such as roof construction, types of commercial roofing materials, and seasonal weather patterns. For instance, single-ply membrane roofs may require more frequent inspections due to their susceptibility to punctures from heavy foot traffic. Additionally, roofs with tapered insulation systems should be inspected after significant temperature fluctuations to ascertain proper drainage.
Timing inspections around installation time can also prove beneficial, as it allows for early detection of any defects in the main types of commercial roofing systems. Furthermore, scheduling professional assessments every 3-5 years complements the bi-annual inspections, providing a thorough evaluation of the roof’s overall integrity. By adhering to a well-planned seasonal inspection schedule, warehouse owners can drastically extend their roof’s lifespan and minimize costly repairs.
Emergency Response Planning
Emergency response planning forms a critical component of extensive roof maintenance scheduling for commercial warehouses. With decades of experience in the field, roofing professionals understand that when a roof comes under stress from severe weather or unexpected damage, a well-prepared plan can make all the difference.
This is especially pivotal for warehouses with wide-ranging roofing systems, including standing seam and slope commercial designs, which may incorporate various types of metal materials coated with aluminum to protect against the sun’s harmful rays.
A thorough emergency response plan should include:
- Detailed protocols for evaluating and addressing different types of roof damage
- Contact information for trusted roofing contractors and emergency services
- Guidelines for temporary repairs to minimize further damage
- Procedures for documenting incidents and repairs for insurance purposes
Connect With Us
Don’t Let Roofing Concerns Overshadow Your Warehouse Operations
Take the first step towards a secure and efficient roofing solution for your warehouse. Our experts are ready to guide you through the process, from selection to installation and beyond. We comprehend the unique challenges warehouses face, including potential hail and wind damage common in Colorado.
Our team specializes in addressing these issues to guarantee long-lasting protection for your facility. Safeguard your investment and achieve optimal performance with our thorough roofing services.
Call (303) 306-8384 now to schedule your personalized consultation and discover the perfect roofing system for your warehouse needs. Let’s build a stronger, more resilient future for your facility together.
Roofing FAQ
What Kind of Roof Is Used in a Warehouse?
Warehouses commonly utilize single-ply membranes like TPO, PVC, and EPDM, as well as modified bitumen and built-up roofing systems. Metal roofing is also popular due to its durability. The choice depends on factors such as cost, installation, and maintenance requirements.
What Is the Best Roof for Commercial Building?
The best roof for a commercial building depends on various factors, including climate, budget, and building use. Popular options include single-ply systems, modified bitumen, built-up roofing, and metal roofing. Each offers unique benefits tailored to specific needs.
What Is the Material of Roofing in Industrial Warehouse?
Common roofing materials for industrial warehouses include single-ply membranes (TPO, PVC, EPDM), modified bitumen, and metal roofing systems. Each option offers unique benefits, balancing factors like cost-effectiveness, durability, and weather resistance to meet diverse industrial needs.
What Is the Most Common for Commercial Roofing?
The most common commercial roofing materials are single-ply membranes like TPO, PVC, and EPDM. These options offer cost-effectiveness, energy efficiency, and easy installation. Modified bitumen, built-up roofing systems, and metal roofing are also popular choices for many businesses.